Аннотация
Потоки углеводородных газов, получаемых в технологиях химических и нефтеперерабатывающих производств, имеющих достаточно высокую температуру, целесообразно охлаждать для выделения из них фракций жидкого углеводородного топлива. В зимний период это возможно путем охлаждения газа технической водой из оборотной системы теплоснабжения, а в летний период, особенно для южных районов страны, необходимы установки для производства искусственного холода. Объект исследования – теплоиспользующие холодильные установки пароэжекторного и абсорбционного типа. Методы исследования – теоретические, путем моделирования рабочих циклов. При охлаждении технологического газа для получения из него жидкого углеводородного топлива с помощью пароэжекторной и абсорбционной холодильных установок технические показатели абсорбционной холодильной установки несколько выше (на 20 … 25 %), чем у пароэжекторной холодильной установки.
Потоки углеводородных газов, получаемых в технологиях химических и нефтеперерабатывающих производств, имеющих достаточно высокую температуру (порядка 60°С и выше), целесообразно охлаждать до 20…35°С для выделения из них фракций жидкого углеводородного топлива. Расчеты показали, что из газа с массовым составом углеводородов и при давлении этого газа 10…11 бар может быть сконденсировано 36…57% по массе жидкого н-бутана и н-пентана. При этом необходимо отводить 150…230 кДж тепла на 1 кг газа. В расчетах использовались справочные данные [1-3].
В зимний период это возможно путем охлаждения газа технической водой из оборотной системы теплоснабжения, а в летний период, особенно для южных районов страны, необходимы установки для производства искусственного холода.
Следует иметь в виду, что на вышеназванных производствах имеются теплогенераторы (котельные установки, печи и т.п.), продукты сгорания на выходе из которых имеют достаточно высокий (300…350°С) потенциал и нуждаются в утилизации. Утилизированное тепло может быть использована для получения искусственного холода.
К числу таких теплоиспользующих холодильных установок (ХУ) относятся пароэжекторные (ПЭХУ) и водоаммиачные абсорбционные (АХУ).
В настоящей работе проводится сравнение основных технических показателей этих двух типов установок применительно к задаче охлаждения технологического углеводородного газа в летний период. Такое сравнение позволит более обоснованно подойти к выбору типа ХУ и для решения подобных задач.
Объект исследования – теплоиспользующие холодильные установки пароэжекторного К абсорбционного типа.
Предмет исследования – рабочие режимы теплоиспользующих холодильных установок пароэжекторного и абсорбционного типа.
Методы исследования – теоретические, путем моделирования рабочих циклов. Условия сравнения технических показателей в ПЭХУ и АХУ Рассмотрены режимы работы типичной технологической линии нефтеперерабатывающих производств [1]:
- расход технологического газа 12 т/ч (состав газа указан выше), его давление 10 бар, температура на входе в испаритель ХУ 60°С;
- расход утилизируемых продуктов сгорания 18•103 м3/ч (примерно 13,5 т/ч при плотности 0,75 кг/м3), их температура 350°С;
- температура технической воды на входе в охлаждаемые элементы ХУ 40°С, на выходе из них 45 °С.
В результате расчетов для каждой ХУ определяются:
- температура конца охлаждения технологического газа;
- температура конца охлаждения продуктов сгорания;
- параметры в характерных точках термодинамических циклов ХУ: давление Рі, температураtі, удельный объемυі, энтальпия hі, массовое паросодержание хі, концентрация аммиака в воде аммиачной смеси (для АХУ) ξі, расходG (приведенный [кг/кг] и абсолютный [кг/с]), скорости потоков (для потоков в проточной части эжектора ПЭХУ);
- холодопроизводительность и тепловой коэффициент ХУ;
- -тепловая нагрузка теплообменных аппаратов и мощности насосов - побудителей циркуляции;
- в поверхности нагрева и габариты теплообменного оборудования;
- в габариты эжекторной группы (для ПЭХУ).
Технические показатели ПЭХУ Принципиальная схема и цикл ПЭХУ представлены на рис.1. В качестве хладагента и рабочего тела приняты вода и водяной пар, как наиболее перспективные для заданного уровня температур [3].
Технологический газ охлаждается в испарителе И от 60 до 35°С за счет полного выкипания в нём (7-10) относительно низкотемпературной (25 °С) пароводяной смеси. При этом от газа отводится тепло и из него конденсируются жидкое углеводородное топливо. Образующиеся в И водяные пары отсасываются и сжимаются (1-2) эжекторами ЭГ за счет кинетической энергии высокотемпературного пара из парогенератора керхер ПГ, реализующейся при расширении этого пара (9-а) в соплах ЭГ. Сжатый до давления конденсации в ЭГ пар (точка 2) охлаждается и конденсируется (2-3-4) в конденсаторе К, отдавая охлаждающей конденсатор технической воде тепло. Сконденсировавшаяся вода (точка 4) разветвляется на два потока: один поток направляется в холодильную часть установки и, после дросселирования (4-7) в ДВ до состояния пароводяной смеси (точка 7) поступает в И для полного выпаривания; другой поток воды сжимается насосом Н до давления парогенератора и направляется в него, где подогревается и кипит (5-8-9) за счёт подвода утилизируемого от продуктов сгорания тепла. Генерируемый в ПГ высокотемпературный пар поступает в ЭГ в качестве энергоносителя для сжатия «холодного» пара из И. Цикл замыкается.
Параметры в характерных точках цикла и основные показатели термодинамической эффективности ПЭХУ представлены в табл.1 и 2. Пароэжекторная группа рассчитывалась по методике, разработанной авторами в ОНАХТ. Цикл рассчитывался по общепринятой методике [3], используя справочные данные [4]. При расчетах принято: коэффициенты скорости в эжекторах ЭГ – сопла рабочего пара 0,96; кольцевого сопла сжимаемого пара 0,9; камеры смешения 0,95; КПД диффузора 0,93; КПД насосов для перекачки воды 0,8.
Пароэжекторная группа. Количество эжекторов – 6. Параметры рабочего пара: температура 140 °C, давление 3,61 бар, степень сухости 1, расход на один эжектор 0,057 кг/с. Параметры отсасываемых водяных паров: температура 25°C, давление 0,032 бар, степень сухости 1, расход на один эжектор 0,036 кг/с.
Параметры смеси паров в камере смешения: температура 23°C, давление 0,028 бар, степень сухости 0,952. Коэффициент эжекции 0,625. Габариты одного эжектора: длина 1,7 м, диаметр 0,3 м.
Оценивались поверхности нагрева и габариты элементов теплообменного оборудования ХУ: парогенератора, конденсатора и испарителя. Расчёты проводились в соответствии с методиками [5].
Парогенератор. Тепловая нагрузка: 860 кВт. Греющая среда: продукты сгорания с расходом 3,74 кг/с. Температуры на входе и выходе 350°С и 144°С, соответственно, давление 1 бар. Нагреваемая среда: вода и водяной пар с расходом 0,342 кг/с. Температуры на входе и выходе 49,1°С и 140°С, соответственно, давление 3,61 бар. Конструкция: прямоточный с кипением внутри оребренных труб с наружным диаметром 50 мм, степень оребрения 13, приведенный коэффициент теплопередачи 280 Вт/(м2•К), поверхность нагрева 58 м2. Габариты: длина 1,6 м, ширина
1,6 м, высота 2,5 м.
Конденсатор. Тепловая нагрузка 1362 кВт. Греющая среда: перегретый и насыщенный конденсирующийся водяной пар с расходом 0,556 кг/с. Температуры на входе и на выходе 89,3 °С и 49,1 °С, соответственно, давление 0,12 бар. Нагреваемая среда: техническая вода с расходом 65 кг/с. Температуры на входе и на выходе 40 °С и 45 °С, соответственно, давление 1 бар. Мощность насоса для прокачки воды 4,1 кВт. Конструкция: противоточный с конденсацией на наружной поверхности труб диаметром 20 мм. Коэффициенты теплопередачи на участке снятия перегрева 30 Вт/(м2•К), на участке конденсации 100 Вт/(м2•К). Поверхность нагрева 258 м2. Габариты: длина 2 м, диаметр 1,6 м.
Параметры в характерных точках цикла ПЭХУ
Испаритель. Тепловая нагрузка 500 кВт. Греющая среда: технологический газ с расходом 3,33 кг/с. Температуры на входе и на выходе 60 °С и 35 °С, соответственно, давление 10 бар. Количество сконденсировался углеводородного топлива 4,31 т/ч. Нагреваемая среда: кипящая пароводяная смесь с расходом 0,214 кг/с, давление 0,032 бар. Конструкция: трубчатый с конденсацией жидких углеводородов в объеме на внешней оребренной поверхности труб диаметром 20 мм (степень оребрения 7) и кипением пароводяной смеси внутри этих труб. Приведенный коэффициент теплопередачи 420 Вт/(м2•К). Поверхность нагрева 60 м2. Габариты: длина 1,8 м, ширина 0,5 м, высота 2,2 м.
Технические показатели АХУ
Принципиальная схема и цикл АХУ представлены на рис. 2. Схема работает на водоаммиачной смеси (хладагент - аммиак, абсорбент - вода). Технологический газ охлаждается в испарителе И от 60 до 32 °С за счёт выкипания в нём (5-6) при минимальном давлении в цикле Р0 относительно холодной (9 °С) парожидкостной аммиачной смеси. При этом от газа отводится теплота и из неё конденсируются жидкие углеводороды. Образующийся в испари-телеИ насыщенный пар аммиака, перегреваясь (6-7) в охладителе жидкости ОЖ, охлаждает жидкий аммиак (3-4), поступающий в охладитель ОЖ из конденсатора К.
Подогретый пар аммиака (точка 7) поступает в абсорбер А, где после барботирования в «слабом» водоаммиачном растворе (точка 11), попадает в А после дросселирования (10-11) в ДВ-2 от максимального давления в цикле до минимального, смешивается с этим «слабым» раствором (точка 12) и абсорбируется им до состояния «крепкого» насыщенного раствора (точка 13). При этом технической водой, охлаждающий абсорбер А, отводится теплота абсорбции. Полученный «крепкий» раствор сжимается в насосе Н (13-14) до давления Р0, подогревается (14-15) в регенеративном теплообменнике ТР за счет охлаждения в нём «слабого» раствора из генератора Г и поступает через ректификационную колонну РК в генератор Г. В генераторе «крепкому» раствору противотоком подводится теплота утилизируемых продуктов сгорания, при этом раствор кипит, его температура повышается, а концентрация по аммиаку уменьшается (15-9). Смесь паров аммиака и воды переменной концентрации, омывая в РК пленки ещё не подогретого в Г и потому более холодного «крепкого» раствора, охлаждается и обогащается по аммиаку за счет частичной конденсации водяного пара. Окончательная очистка смеси паров осуществляется в дефлегматоре при отводе от него (1-2) технической водой теплоты дефлегмации. Образовавшееся при этом флегма (смесь сконденсировавшейся воды и части аммиака, состояния близкого к точке 8) возвращаются обратно в Г. Очищенный аммиачный пар конденсируется (2-3) в К за счет отвода к охлаждающей его технической воде теплоты конденсации. Сконденсировавшийся жидкий аммиак переохлаждается в ОЖ, дросселируется (4-5) в ДВ-1 и поступает в качестве хладагента в И. Цикл замыкается.
Параметры в характерных точках цикла и основные показатели термодинамической эффективности АХУ представлены в табл. 3 и 4. Расчеты проводились в соответствии с методиками [3, 6], использовались справочные данные [7].
Аналогично ПЭХУ оценивались поверхности нагрева и габариты элементов теплообменного оборудования АХУ. Результаты приведены ниже.
Генератор. Тепловая нагрузка 1027 кВт. Греющая среда: продукты сгорания с расходом 3,74 кг/с, давление 1 бар. Температуры на входе и на выходе 350 °С и 100 °С, соответственно. Нагреваемая среда: кипящий водоаммиачный раствор с расходом 1,258 кг/с; концентрация аммиака 0,483 кг/кг на входе и 0,113 кг/кг на выходе; температуры на входе и на выходе 93,4 °С и 179,2 °С, соответственно; давление 20 бар.
Конструкция: принят аппарат с пленочной раздачей раствора внутри вертикальных оребренных труб наружного диаметра 120 мм (коэффициент оребрения 13), поперечно омываемых продуктами сгорания. Такая конструкция позволяет организовать противоточную схему тепломассообмена с отводом генерируемого внутри труб водоаммиачного пара переменной концентрации аммиака в ректификационную колонну.
Возможны и другие варианты, например, 3-4 ступенчатая конструкция с кипением в каждой ступени в объеме соответствующего аппарата и сбором пара различной концентрации их аппаратов всех ступеней в общую ректификационную колонну.
Для принятой конструкции: приведенный коэффициент теплопередачи 286 Вт/(м2•К), поверхность нагрева 71 м2. Габариты: высота 2,5 м, диаметр 2,4 м.
Абсорбер. Тепловая нагрузка 952 кВт. Греющая среда: водоаммиачная парожидкостная смесь с расходом 1,258 кг/с. Температуры на входе и на выходе 94,1°С и 50°С, соответствен-но. Нагреваемая среда: кипящий водоаммиачный раствор с расходом 1,258 кг/с; концентрация пара на входе 0,907 кг/кг, раствора на входе 0,23 кг/кг и 0,483 кг/кг на выходе; давление 6 бар. Конструкция: противоточный змеевиковый с движением воды внутри труб диаметром 20 мм. Коэффициент теплопередачи 500 Вт/(м2•К). Поверхность нагрева 76 м2. Габариты: длина 1,6 м, диаметр 1,5 м.
Конденсатор. Тепловая нагрузка 554,5 кВт. Греющая среда: конденсирующийся пар аммиака с расходом 0,525 кг/с, температуры на входе и на выходе 49,4 °С, давление 20 бар. Нагреваемая среда: техническая вода с расходом 26,4 кг/с, температуры на входе и на выходе 40 °С и 45 °С, соответственно, давление 1 бар.
Конструкция: противоточный с конденсацией на наружной поверхности труб диаметром 20 мм. Коэффициент теплопередачи 1000 Вт/(м2•К), поверхность нагрева 80 м2. Габариты: длина 1,5 м, диаметр 1,2 м.
Дефлегматор. Тепловая нагрузка 104,5 кВт. Греющая среда: водоаммиачный пар с расходом 1,04 кг/с, температуры на входе и на выходе 93,4 °С и 49,4°С, соответственно, концентрации на входе и на выходе 0,98 и 1,0, соответственно, давление 20 бар. Нагреваемая среда: техническая вода с расходом 5 кг/с, температуры на входе и на выходе 40 °С и 45 °С, соответственно, давление 1 бар.
Конструкция: трубчатый аппарат с конденсацией флегмы на наружной поверхности оребренных труб диаметром 20 мм (степень оребрения 7). Приведенный коэффициент теплопередачи 412 Вт/(м2•К), поверхность нагрева 11 м2. Габариты: длина 1,6 м, диаметр 0,8 м.
Испаритель. Тепловая нагрузка 584 кВт. Греющая среда: технологический газ с расходом 3,33 кг/с. Температуры на входе и на выходе 60 °С и 32 °С, соответственно, давление 10 бар. Количество сконденсировался углеводородного топлива 5,26 т/ч. Нагреваемая среда: кипящая парожидкостная аммиачная смесь с расходом 0,525 кг/с, температурами на входе и на выходе 9,3 °С, давление 6 бар.
Конструкция: трубчатый с конденсацией жидких углеводородов в объеме на внешней оребренной поверхности труб диаметром 20 мм (степень оребрения 7) и кипением аммиака внутри этих труб. Приведенный коэффициент теплопередачи 420 Вт/(м2·К). Поверхность нагрева 40 м2. Габариты: длина 1,5 м, ширина 0,3 м, высота 2,2 м.
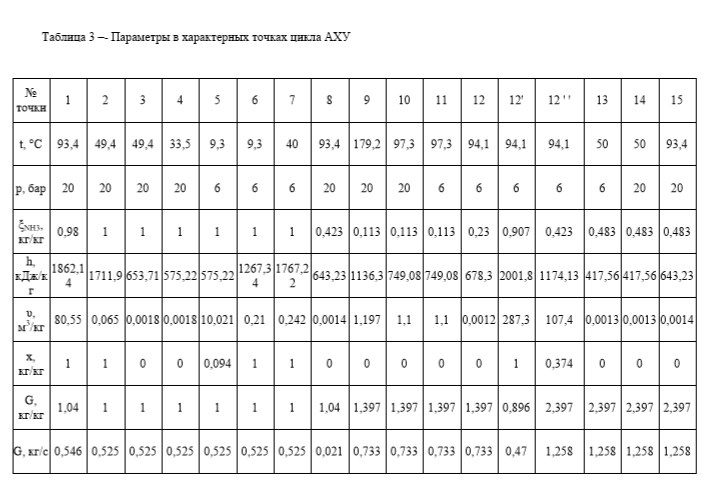
Параметры в характерных точках цикла АХУ
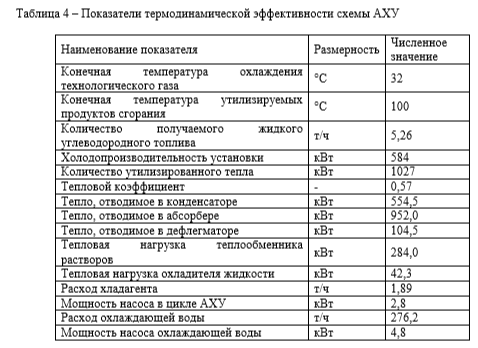
Показатели термодинамической эффективности схемы АХУ
Теплообменник растворов. Тепловая нагрузка 284 кВт. Греющая среда: слабый водо-аммиачный раствор с концентрацией аммиака 0,113 кг/кг, расходом 2,64 т/ч, температуры на входе и на выходе 179,2 °С и 97,3 °С, соответственно, давление 20 бар. Нагреваемая среда: крепкий водоаммиачный раствор с концентрацией аммиака 0,483 кг/кг, расходом 1,258 кг/с, температуры на входе и на выходе 50 °С и 93,4 °С, соответственно, давление 20 бар.
Конструкция: трубчатый противоточный с нагревом крепкого раствора на наружной поверхности труб диаметром 10 мм. Коэффициент теплопередачи 500 Вт/(м2•К), поверхность нагрева 9 м2. Габариты: длина 1 м, диаметр 0,4 м.
Охладитель жидкости. Тепловая нагрузка 42,3 кВт. Греющая среда: жидкий аммиак с расходом 0,525 кг/с, температуры на входе и на выходе 49,4 °С и 33,5 °С, соответственно, давление 20 бар. Нагреваемая среда: перегретый пар аммиака с расходом 0,525 кг/с, температуры на входе и на выходе 9,3 °С и 40 °С, соответственно, давление 6 бар.
Конструкция: трубчатый противоточный с нагревом пара на наружной поверхности оребренных труб диаметром 15 мм (степень оребрения 7). Приведенный коэффициент тепло-передачи 210 Вт/(м2•К), поверхность нагрева 16 м2. Габариты: длина 1 м, диаметр 0,7 м.
Полученные выше данные позволяют провести сопоставление основных технических показателей ПЭХУ и АХУ применительно к цели охлаждения технологического углеводородного газа.
Результаты технического анализа технических показателей ПЭХУ И АХУ
Результаты сопоставления показателей сведены в таблице 5.
Анализ результатов табл. 5 показал, что получение большего количества жидкого углеводородного топлива в варианте с АХУ (при примерно равных тепловых коэффициентах в обоих типах установок) связано с:
- в возможностью более глубокого охлаждения технологического газа (температура кипения аммиака в испарителе АХУ равна 9 °С, в то время как в испарителе ПЭХУ вода кипит при 25 °С);
- в возможностью более глубокой утилизации продуктов сгорания (до 100 °С) ввиду переменности температуры кипения водоаммиачного раствора в парогенераторе АХУ;
- меньшие суммарные поверхности нагрева теплообменного оборудования (на 25%) в АХУ, несмотря на большее количество теплообменных аппаратов, это связано с отводом теплоты к охлаждающей воде не только в конденсаторе, как это имеет место в ПЭХУ, но и в абсорбере и дефлегматоре, осуществляющийся при больших, чем в конденсаторе, температурных напорах.
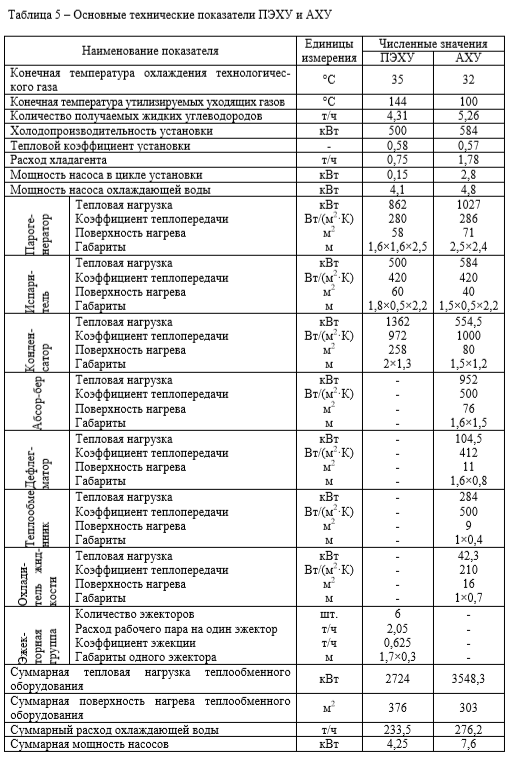
Основные технические показатели ПЭХУ и АХУ
Выводы При охлаждении технологического газа для получения из него жидкого углеводородного топлива с помощью пароэжекторной и абсорбционной холодильных установок технические показатели АХУ (возможность более глубокого охлаждения газа, большее количество получаемого топлива, меньшие суммарные поверхности нагрева теплообменных аппаратов) несколько выше (на 20 – 25 %), чем ПЭХУ.
Тем не менее, ввиду определенной сложности АХУ (большее число элементов оборудования, более высокий уровень давлений 6 - 20 бар, применение более агрессивного хладагента – аммиака) окончательный выбор типа холодильной установки для этих целей может быть сделан, исходя из условий и возможностей конкретного производства.
Список литературы
- Варгафтик, Н. Б. Справочник по теплофизическим свойствам газов и жидкостей / Н. Б. Варгафтик. – М: Наука, 1972. – 720 с.
- Павлович, Н. В. Справочник по теплофизическим свойствам природных газов и их компонентов / Н. В. Павлович. – М-Л: Госэнергоиздат, 1962. – 120 с.
- Кошкин, Н. Н. Холодильные машины / Под ред. Кошкина Н. Н. – М.: Пищевая про-мышденность, 1973. – 512 с.
- Ривкин, С. Л. Термодинамические свойства воды и водяного пара: Справочник / С. Л. Ривкин, А. А. Александров. Рек. Гос. службой стандартных справочных данных, 2-е изд., перераб. и доп. – М.: Энергоатомиздат, 1984. – 80 с.
- Исаченко, В. П. Теплопередача / В. П. Исаченко, В. А. Осипова, А. С. Сукомел. – М.:
Энергия, 1975. – 488 с. - Бадылькес, И. С. Абсорбционные холодильные машины / И.С. Бадылькес, Р.Л. Данилов.
– М.: 1966. – 356 с. - Богданов, С. Н. Холодильная техника. Свойства веществ / С.Н. Богданов, О.П. Иванов, А. В. Куприянова. – М. : Агропромиздат, 1985. – 208 с.
Авторы: Титлов А.С.1, д.т.н., профессор Сагала Т.А.2, к.т.н, старший препод. Дьяченко Т.В.3, к.т.н., доцент Артюх В.Н.4, аспирант Магурян Н.С.5, студентка